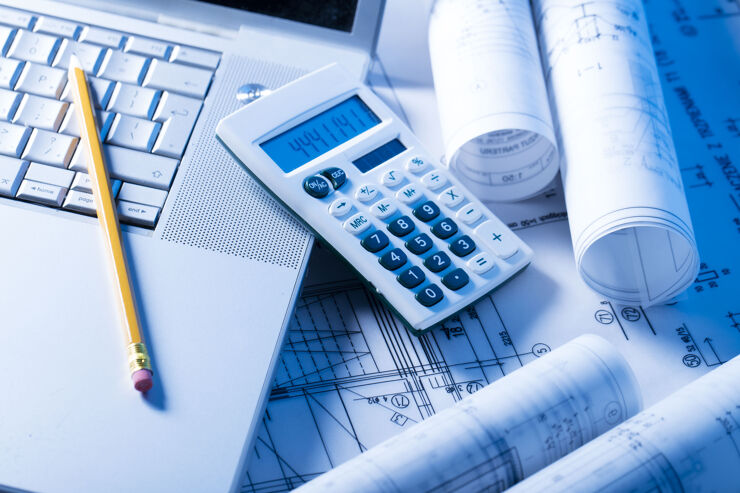
Key Points
- A defect is a term defined in the NEC4 ECC.
- The ECC includes processes for notifying and correcting defects.
- Defects can be accepted by agreement between the contractor and project manager.
- The contractor is liable for uncorrected defects, whether or not the client provides access
Defects are one of the most common causes of disputes in the engineering and construction industry (Nazzini and Kalisz, 2022). A recent survey suggests that up to 30% of work in the UK construction sector involves the correction of defects (Johnson, 2022). This article explains how defects are defined and managed in the NEC4 Engineering and Construction Contract (ECC) and explores liability for uncorrected defects.
What is a defect?
NEC4 ECC clause 11.2(6) defines a defect as:
- ‘a part of the works which is not in accordance with the Scope or
- a part of the works designed by the Contractor which is not in accordance with the applicable law or the Contractor’s design which the Project Manager has accepted.’
This contractual definition is limited to defects that arise from the fault of the contractor. A fault in the client’s design which the contractor builds is not a defect and is treated as a client liability (clause 80.1). The first bullet point of clause 11.2(6) reflects the contractor’s general obligation to provide the works in accordance with the scope (clause 20.1).
The second bullet point affirms that the contractor is required to construct the works in accordance with the law, such as building regulations, and its accepted design. If the contractor wants to change its design, then it would need to re-submit the design to the project manager and gain acceptance. Clause 14.1 clarifies the position that the project manager’s acceptance of the contractor’s design does not change the contractor’s liability for its design.
A similar definition exists in the NEC4 Engineering and Construction Subcontract (ECS), with the term ‘Scope’ replaced by ‘Subcontract Scope’. Consequently, a defect in the main contract is not necessarily a defect under the subcontract.
Notifying and correcting defects
The obligation to notify a defect is that of the supervisor and the contractor and is triggered when either becomes aware of a defect (clause 43.2).
However, failure by the supervisor to notify the contractor of a defect does not relieve the contractor from its obligation to correct it (clause 44.1). While the obligation to notify a defect ceases after the defects date (typically 52 weeks after completion), the contractor’s liability for defects does not.
The definition of a defect does not differentiate between incomplete work and work that does not comply with the scope. In practice, the supervisor will need to apply judgement when deciding to notify a defect for work that is incomplete or non-compliant as opposed that which is work in progress. Reference to the accepted programme and consultation with the contractor should avoid unnecessary or inappropriate notifications.
The contractor is required to correct a notified defect before the end of its defect correction period (clause 44.2). The defect correction period, stated in contract data, may include different periods for different types of defect or defects in different parts of the works. It is easy for the contractor to be ‘timed out’ on a short defect correction period, so contract drafters need to consider these periods carefully.
The point at which the defect correction period commences depends on two factors: when the defect is notified and when the client allows access for the contractor after take over. If a defect is notified before completion, its defect correction period begins at completion. If a defect is notified after completion, the period begins when the defect is notified (clause 44.2).
However, for a defect in a part of the works that the client has taken over, the start of the defect correction period is delayed until such time the client allows access for the contractor (clause 44.4). It should be noted that the client may exercise its right to take over before completion. Conversely, if the contract data states the client is not required to take over before the completion date, the client is required to take over no later than 2 weeks after completion.
Payment for correcting a defect
It may come as a surprise to some to find that NEC4 ECC allows the contractor to recover its costs for correcting a defect. For a fixed-price contract (Options A and B), it is probable that the contractor’s price includes some risk allowance for correcting defects. Any allowance for this is rarely transparent in a fixed-price contract and ultimately the client pays the contractor the price agreed for an item irrespective of the presence of a defect and the cost incurred by the contractor.
For cost-reimbursable contracts (Options C, D, E and F), the contractor is entitled to be paid for correcting defects providing it is not deemed to be a disallowed cost (clause 11.2(26)). Disallowed cost includes the cost of correcting defects after completion and not complying with a constraint stated in the scope as to how the contractor provides the works. Exceeding the target (Options C and D) may also result in the contractor paying for some or all of its costs incurred in correcting defects.
Certifying completion with defects
Completion may be deemed to have been achieved even when there is a defect. Clause 11.2(2) treats the works as complete providing a notified defect does not prevent the client from using the works or others from doing their work.
The approach reflect the position taken by UK common law in that the works would, for all practical purposes, be considered complete if they are capable of their intended use (Westminster Corporation v. J Jarvis & Sons Ltd [1970] 1 WLR 637) and the defect is not ‘more than trifling’ (Mears Ltd v. Costplan Services (South East) Ltd [2019] EWCA Civ 502, [80]).
Accepting a defect
NEC4 ECC provides a mechanism for accepting a defect. The process may be initiated by the contractor or the project manager by way of a proposal to change the scope so the defect does not have to be corrected (clause 45.1). The proposal is followed by the contractor’s quotation submitted to the project manager for acceptance, providing both the contractor and project manager are willing to accept the defect. The contractor’s quotation must represent a reduction in prices or an earlier completion date or both. A defect which is not in accordance with the applicable law should not be accepted.
Accepting a defect provides compensation for the client but the contract does not treat it as a compensation event. This means the rules of defined cost do not apply, nor is the project manager entitled to carry out its own assessment. It could be said that accepting a defect is a negotiated agreement. If the contractor’s quotation is not accepted, the defect remains uncorrected. Once accepted the matter is no longer treated as a defect. It is recommended the project manager consults with the client and the supervisor before embarking on any agreements.
Remedies for uncorrected defects
The contractual remedy for an uncorrected defect depends on whether or not the client allows access for the contractor to correct the defect. Clause 46.1 explains that if the client has given access and the contractor fails to correct the defect within its defect correction period, then the contractor becomes liable for the amount assessed by the project manager for the client to have the defect corrected by others.
If the client does not provide access, the contractor is still liable for the cost of correcting the defect. However, the project manager’s assessment must be based on what it would have cost the contractor to correct the defect (clause 46.2). Clause 44.4 represents an expectation that the client will provide access for the contractor to correct a defect but does not go as far as stating an express obligation to do so.
Common law informs that if a contractor is not afforded the opportunity to correct a defect, the contractor’s liability to the client for the uncorrected defect is limited to that of the contractor’s rectification costs (Pearce & High Ltd v. Baxter [1999] BLR 101). Clause 46.2 is therefore generally considered to be consistent with UK common law.
Liability for patent and latent defects?
The terms ‘patent defect’ and ‘latent defect’ are often talked about but are not terms used in NEC contracts. A patent defect is one that can be seen or is apparent upon inspection by a person with relevant experience or expertise (AMEC Foster Wheeler Group Ltd v. Morgan Sindall Professional Services Ltd [2016] EWHC 902 (TCC) [50]). In NEC4 ECC, a test or inspection required by the scope or applicable law (clause 41.1) which showed a defect would be classed as a patent defect.
A latent defect is one that exists but is hidden to the extent that it would not be discoverable from an inspection that the defendant might reasonably anticipate the article would be subjected to (Baxall Securities Ltd v. Sheard Walshaw Partnership [2002] BLR 100, 108 [46]).
Whether a defect is classed as patent or latent could be significant in determining when the applicable statutory limitation period begins. If secondary option X18 is included in the NEC4 ECC, the statutory limitation period in connection with the contractor’s liability for a defect may be reduced by stating the ‘end of liability date’ in the contract data.
Clause X18.6 states, ‘The Contractor is not liable to the Client for a matter unless details of the matter are notified to the Contractor before the end of the liability date’. However, use of clause X18 does not necessarily preclude the client from bringing a claim against the contractor after the end of the liability date (e.g. under the UK Limitation Act 1990).
Conclusion
Defects are an inevitable part of construction projects. NEC4 ECC provides a framework of rules for notifying, correcting and dealing with uncorrected defects. Clear and concise drafting of the scope, appropriate selection of subcontractors and following the contract will reduce the risk of disputes and costs to both parties.
References
Johnson T (2022) UK construction industry spends more on error than its annual profits, New Civil Engineer, 13 September, https://www.newcivilengineer.com/latest/uk-constructionindustry-spends-more-on-error-than-its-annualprofits-13-09-2022
Nazzini R and Kalisz A (2022) 2022 Construction Adjudication in the United Kingdom: Tracing trends and guiding reform, Centre of Construction Law & Dispute Resolution, King’s College London, https://www.kcl.ac.uk/construction-law/assets/2022-construction-adjudication-in-theunited-kingdom-tracing-trends-and-guidingreform.pdf