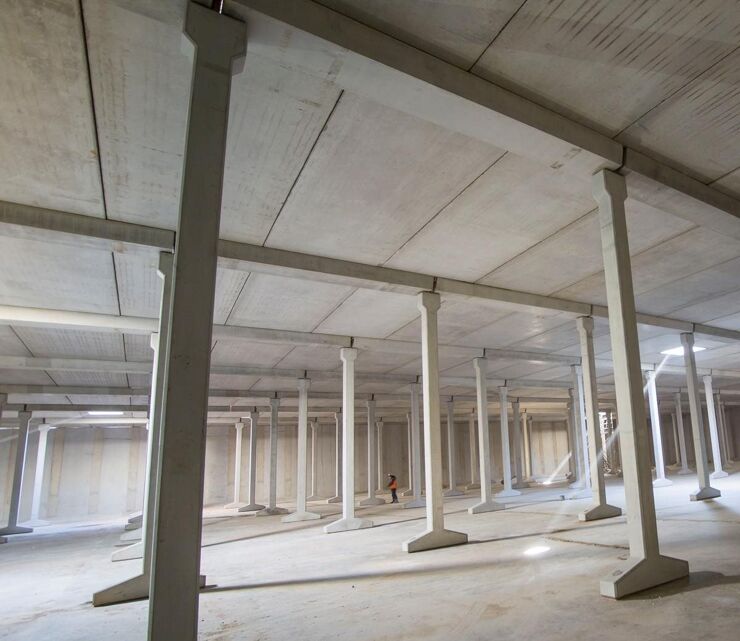
A £28 million, NEC-procured resilience project was completed for Anglian Water in May 2017 at Grafham Water Treatment Works near Huntingdon in Cambridgeshire.
The five-year project involved significant reuse and adaptation of existing assets, which saved £30 million and reduced embodied carbon dioxide content by 50%. This resulted in the project winning the Carbon Reduction Project of the Year Award at the 2017 British Construction Industry Awards.
The designer was Mott MacDonald and construction work was let to JN Bentley under an NEC3 Engineering and Construction Contract Option C (target contract with activity schedule). Anglian Water was client and project manager.
The treatment works supplies water to 829,000 people including all of Northampton, Huntingdon and Bedford. It was estimated that 614,000 people would suffer if there was a serious breakdown at the plant. Anglian Water’s 2010–2015 asset management programme therefore included a scheme to improve resilience.
The scheme proposed building a new 37km long 1100mm diameter supply pipeline from the Hannington covered reservoir to the works. However, the route faced significant challenges including river crossings, urban areas and a site of special scientific interest.
Through collaborative working, the project team identified an alternative solution in which flows could be reversed in the existing 36km, 900mm diameter, 50-year-old pipeline which supplies water from the works to Hannington. During a works outage, water could be supplied from Hannington to a new 44 megalitre covered service reservoir next to the works. A ground-breaking flow-reversal trial in 2012 proved the viability of the solution.
Digital Engineering and DFMA
Extensive use of digital engineering and design for manufacture and assembly (DfMA) techniques helped ensure the complex project – split over 15 sites – remained on budget and on programme. Four-dimensional (physical plus time) modelling of construction sequencing was undertaken in Navisworks and walk-through models using Revitzo were used to discuss design changes and identify any clashes with existing operations. Civil 3D was also used to optimise earthworks.
Work sites included four booster pumping stations along the existing pipeline – ranging from 8 l/s to 160 l/s – to ensure the required reverse flow rates. All four were built using DfMA techniques. One of the largest sites was for the new service reservoir, which also included a new pumping station of 1,250 l/s. The reservoir walls, columns, beams and roof planks were constructed using with precast concrete components manufactured off site – making it the largest precast concrete service reservoir in the UK.
The 200 wall panels were installed in less than four weeks and stitched with dual concrete pours. To ensure full watertightness across the joints, expanding hydrophilic strips were placed in a rebate cast into the pre-cast elements at interfaces with in situ concrete. The sides of reservoir were covered with excavated material to reduce the visual impact and avoid materials being moved off site.
The DfMA approach also minimised health and safety risk, such as by reducing working at height and the number of personnel on site. The health and safety culture extended to the whole supply chain through adopting NEC’s ‘one team’ collaborative approach. In 275,000 man hours there were zero reportable incidents.
Fully Integrated Team
Anglian Water project manager Annabelle Kirkby says the collaborative ethos of NEC was reinforced with Anglian Water alliance agreement. ‘By having a fully integrated, co-located team it allowed us to develop a trust and understanding which can often take years to form. Our approach of projects being outcome driven, rather than engineering for the sake of engineering allowed us to challenge convention and push the boundaries of what is possible within the UK water industry.
‘ECC Option C provides a platform from where all parties can contribute and reap the benefits. Innovative solutions, such as our reuse of existing infrastructure across a 600km2 area as opposed to taking the simpler option of building new assets, can become the norm. With NEC’s partnering approach and open-minded clients, contractors, sub-contractors and designers, we are able to work ever closer, developing deeper and longer-term relationships.’
Due to unexpected complexities involved at a framework incentive level, Kirkby says Anglian Water ultimately completed the project by changing the contract to an ECC Option A (target contract with activity schedule) by mutual agreement with the contractor, which simplified final account settlement at alliance agreement level. ‘We believe the new NEC4 Alliance Contract will be even better suited to our needs and we look forward to working with it,’ she says.
Benefits of Using NEC
- NEC collaborative ethos complements alliancing approach and leads to deeper and longer-term relationships.
- ECC Option C provides a platform from where all parties can contribute innovative solutions and reap the benefits.
- NEC facilitates the use of digital engineering and design for manufacture and assembly techniques, enabling projects to be delivered more efficiently and safely.