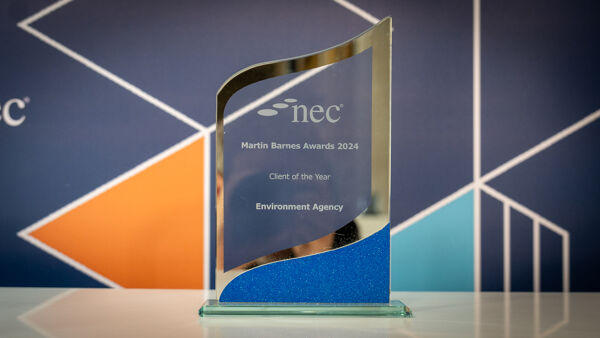
Martin Barnes Awards
The Martin Barnes Awards recognise excellence in project delivery and showcase examples of good practice through collaboration from across the world.
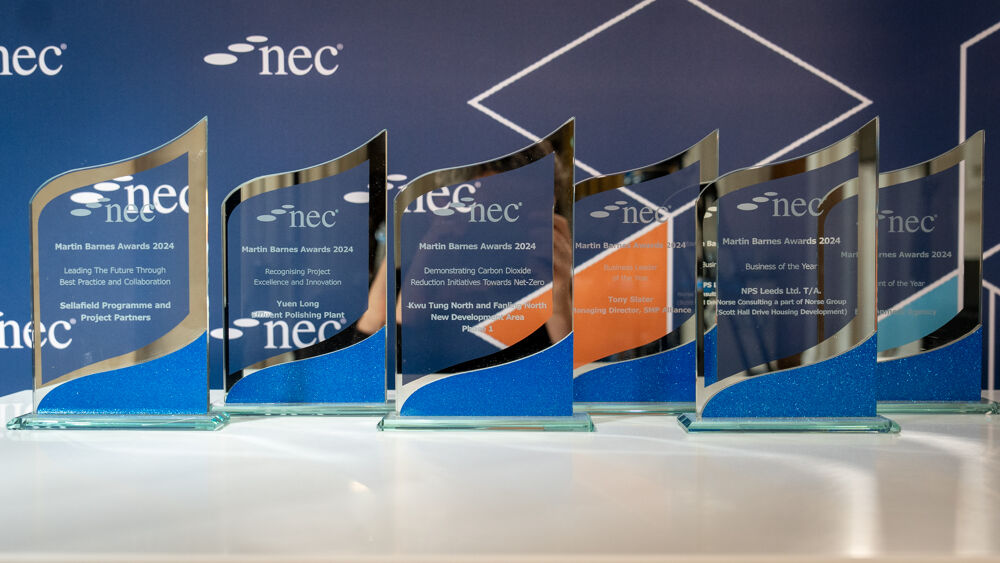
Our winners
2025 Shortlist
Project Excellence and Innovation
- Relocation of Sha Tin Sewage Treatment Works to Caverns
- Fanling Bypass Eastern Section (The Transformative Vehicular Bridge Rotation above a Major Railway Line in Hong Kong)
- Destiny Bridge & The New Kingsway
Future-focused Collaboration
- Framework Contracts for Ground Investigation
- Project and Contract Management Training
- National Emergency Area Retrofit Programme
Climate Change Initiatives
- Tung Chung East District Cooling System
- Retrofitting of Noise Barriers Projects
- Hong Kong’s new Effluent Polishing Plants
- Implementation of Shek Wu Hui Water Reclamation Plant
Client of the Year
- Drainage Services Department, The Government of the Hong Kong Special Administrative Region of the People’s Republic of China
- Perth and Kinross Council
- Escuelas Bicentenario (Bicentennial Schools)
Professional Services of the Year
- Binnies Hong Kong Limited
- TYFRON Solutions Limited
- Koulu JV (Mace and Gleeds)
Contractor of the Year
- Build King Civil Engineering Limited
- Enza Construction
- GRAHAM
Individual Excellence Award
- Diane Dickson, Commercial Director & Doctoral Researcher, MAK Contracting Ltd
- Patrick Finnegan, Principal Engineer – NEC Supervisor and Project Manager, Arup
- Francis Leong, Vice President, AECOM Asia Company Limited
- Peter Winnicott, Commercial and Procurement Director, SMP Alliance (Balfour Beatty)
Distinguished Contribution Award
- Augusto Gutierrez, Peru Country Director, Gleeds
- KY Lo, NEC Tutor
- Richard Patterson, Procurement and NEC Specialist, Mott MacDonald
- Tony HO, Deputy Secretary for Development (Works), The Development Bureau (DEVB), the Government of the Hong Kong Special Administrative Region
Our award categories
Project Excellence and Innovation
This award recognises ground-breaking innovation, inventive solutions and best practice. Entries must demonstrate their creativity in rethinking conventional approaches when tackling complex challenges that has led to transformative change and delivered measurable values in areas such as infrastructure, natural capital, and organisational goals.
Future-focused Collaboration
This award recognises the best in collaborative efforts to develop new solutions to real-world technical challenges and to address social and environmental issues.
Climate Change Initiatives
This award recognises projects that demonstrate sustainable practices and positive societal impact, taking responsibility for minimising potential harms and maximising environmental benefits to help reduce the impact of climate change.
Client of the Year
This category seeks to recognise the organisations that commission projects and can prove their excellence as an exemplary client. They must demonstrate exceptional leadership and vision in fostering sustainability, growth, quality, value, and innovation. It celebrates those who actively drive positive change and inspire progress in their industries.
Professional Services of the Year
This award honors consultancies, advisory firms, and digital solution providers delivering transformative impact through innovation, client and end users’ satisfaction, and leadership in sustainability. It highlights organisations that set the standard for excellence in professional services. Where partners have worked towards common goals, can demonstrate improved performance, and should highlight how their collaboration and integration has resulted in a better outcome for all parties.
Contractor of the Year
This award recognises contractors and subcontractors who set new benchmarks in project delivery by embracing sustainability, innovation, and exceptional efficiency. It celebrates those going beyond conventional practices to deliver outstanding results and promote sustainable ambitions.
Individual Excellence Award
This award celebrates individuals who have demonstrated exceptional creativity, leadership, and innovation in implementing NEC principles. It recognises significant recent contributions that have set new standards of excellence, fostered collaboration, and achieved tangible results in projects and initiatives.
Distinguished Contribution Award
This award honours members who have significantly advanced the adoption and best practices of NEC principles. It recognises their exceptional leadership and dedication in driving collaboration, efficiency and sustainability, leaving a lasting legacy in the NEC community and the wider society.
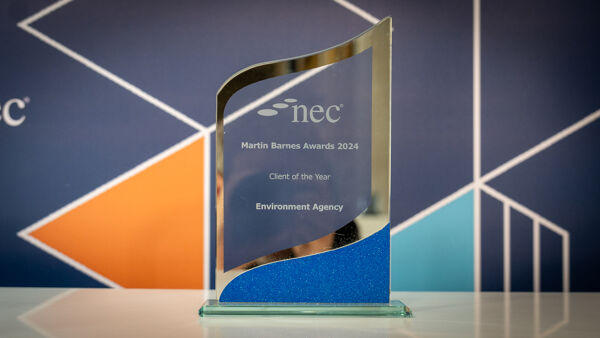
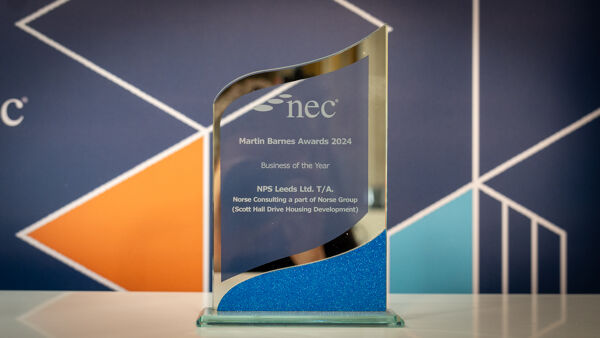
NPS Leeds Ltd. a part of Norse Group (Scott Hall Drive Housing Development)
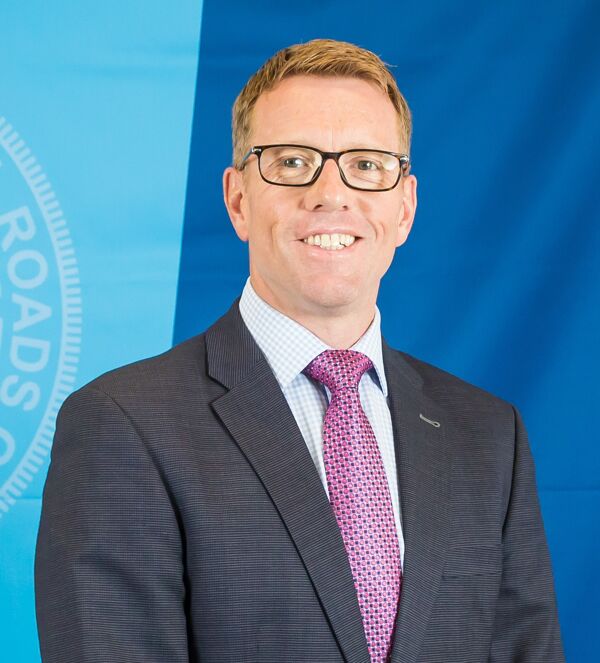
Tony Slater, Managing Director
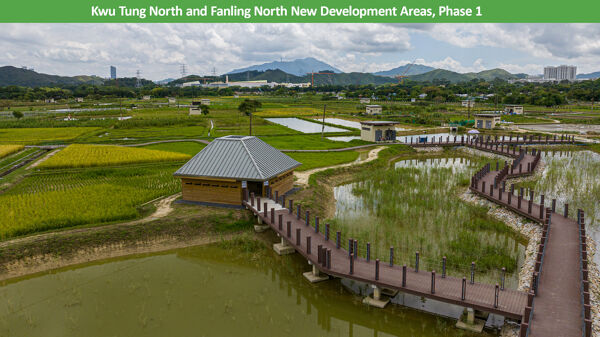
Kwu Tung North and Fanling North New Development Area Phase 1
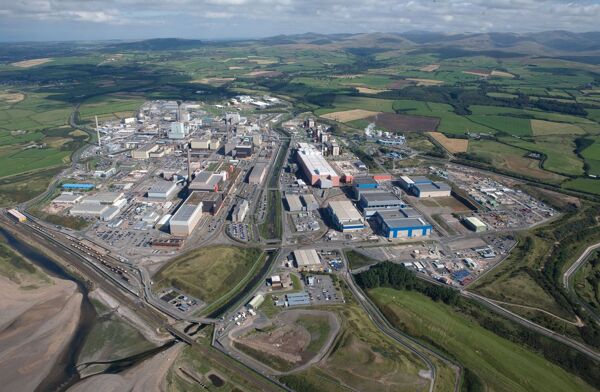
Sellafield PPP
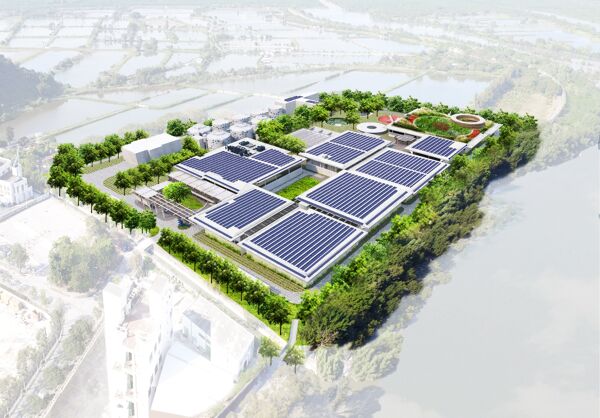
Yuen Long Effluent Polishing Plant
2024 Shortlist
Recognising project excellence and innovation
-
Yuen Long Effluent Polishing Plant
- Universal Accessibility Projects
- Cross Bay Link, Hong Kong
Leading the future through best practice and collaboration
-
Sellafield PPP
- The Palabora Lift II Project
- Development of Lok Ma Chau Loop
Demonstrating carbon dioxide reduction initiatives towards net-zero
-
Kwu Tung North and Fanling North New Development Area Phase 1
- Scott Hall Drive Housing Development
- Collaborative Delivery Framework (extension)
Business Leader of the Year
-
Tony Slater, Managing Director
- Tim Leung, Director of Business Development
- Diane Dickson, Commercial Director
Client of the Year
-
Environment Agency
- MTR Corporation Limited
- Civil Engineering and Development Department, the Government of the Hong Kong Special Administrative Region of the People’s Republic of China
Our award categories
Recognising project excellence and innovation
This award recognises the most innovative projects undertaken including but not limited to new buildings and development, city development and infrastructure, retrofitting programmes, energy efficiency upgrades, smart grid applications, power plants, transport and water infrastructure and natural capital initiatives. More Info.
Leading the future through best practice and collaboration
This award is open to entrepreneurs, developers and organisations that have created or refined a particular project, solution or procurement model which promises to deliver significant economic, environmental and social improvement and best practice. The project also needs to demonstrate effectively collaboration with suppliers/partners or by collective initiatives and partnerships. More info.
Demonstrating carbon dioxide reduction initiatives towards net-zero
This award is open to entrepreneurs, developers and organisations that have created or refined a project, solution (e.g. through contracts) or business model which holds the potential to decarbonise business and drive towards net-zero, without compromising ethics, social contributions, economics and future generations along the way. More info.
Business Leader of the Year
This award is for inspiring leaders who are leading from the top, such as chief executives, directors, and other senior executives. Recognising leadership in enhancing the organisation strategies through mitigating risk and deploying people, technology, processes, systems, engaging stakeholders and industry wide engagement, driving positive change, improving performance, and sparkling innovative ideas actions in their industry and beyond. More info.
Client of the Year
This award recognises organisations that have led the commissioning of projects. It celebrates the impact that those projects have had or will have on improving the lives. It is also open to any consultancy or advisory firm that has delivered substantial and quantifiable improvements of their clients in helping them drive significant changes to achieve sustainable ambitions and going above and beyond normal practice to deliver tangible results. More info.
Business of the Year
Recognising an organisation's environmental, social and financial performance being pushed to new heights in achieving a sustainable future. More info.
Fire Station/Ambulance Depot with Departmental Quarters and Facilities in Area 72, Tseung Kwan O
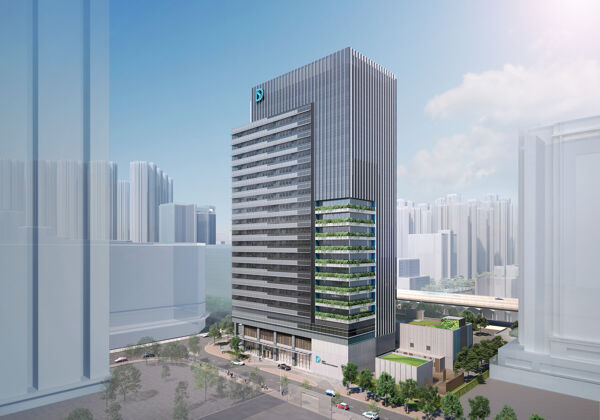
Cheung Sha Wan Sewage Pumping Station
Sha Tau Kok Sewage Treatment Works Expansion
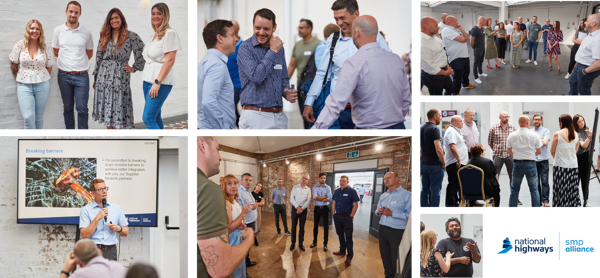
SMP Alliance
Arup-Mott MacDonald JV
NHS ProCure 23 Framework
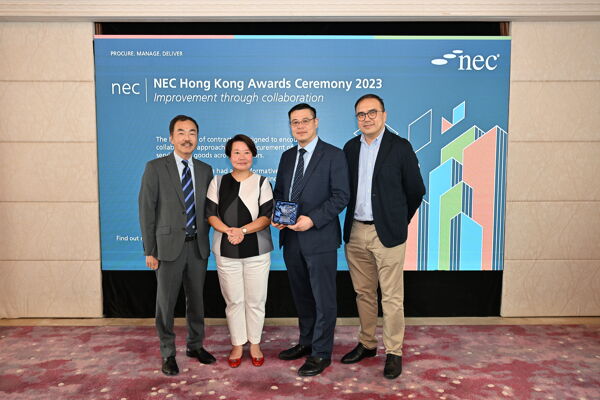
5 Years Term Services Contract (Package C)
Improvement to Dongjiang Water Mains P4 at Sheung Shui and Fanling
SMP Alliance
2023 Shortlist
NEC Transport Contract of the Year
-
SMP Alliance
- Fanling Bypass Eastern Section
- National Highways Area 4 Interim CWF
NEC Water Contract of the Year
-
Improvement to Dongjiang Water Mains P4 at Sheung Shui and Fanling
- Advanced Water Recycling Centre
- Yuen Long Effluent Polishing Plant
NEC Building/FM Project of the Year
-
Cheung Sha Wan Sewage Pumping Station
- The Scottish Government - Contract Support
- Hospital Authority Supporting Services Centre
- Management and Maintenance of Expressways and High Speed Roads (West) in Hong Kong
NEC Sustainability Award of the Year
-
Fire Station/Ambulance Depot with Departmental Quarters and Facilities in Area 72, Tseung Kwan O
- Anderson Road Greywater Treatment Plant
- Kwu Tung North and Fanling North New Development Area
NEC Energy Contract of the Year
-
5 Years Term Services Contract (Package C)
NEC Client of the Year
-
NHS ProCure 23 Framework
- New Plymouth District Council, New Zealand
- Highways Department, HKSARG
NEC Contract Innovation of the Year
-
Sha Tau Kok Sewage Treatment Works Expansion
- Introduction of new NEC Clause
- Site Formation and Infrastructure Works for Public Housing Developments at Kam Tin South, Yuen Long – Phase 1
NEC Contractor of the Year
-
SMP Alliance
- China Railway Construction Corporation – Kwan Lee – Paul Y . JV
- The Jardine Engineering Corporation
NEC Consultant of the Year
-
Arup-Mott MacDonald JV
- AECOM Asia Company Ltd (Shek Wu Hui Polishing Plant)
- Lendlease
Our award categories
NEC Transport Contract of the Year
An award for any project procured in the transport sector under any NEC Contract. The contracts can be in progress (as long as at least one year has passed). Candidates should give a description of best practice collaboration achieved on their NEC project(s) with particular emphasis on clause 10.1 (NEC3) or 10.2 (NEC4).
NEC Water Contract of the Year
An award for any project procured in the water sector under any NEC Contract. The contracts can be in progress (as long as at least one year has passed). Candidates should give a description of best practice collaboration achieved on their NEC project(s) with particular emphasis on clause 10.1 (NEC3) or 10.2 (NEC4).
NEC Building/FM Project of the Year
An award for any project procured in the building and/or facilities management sector under any NEC Contract. The contracts can be in progress (as long as at least one year has passed). Candidates should give a description of best practice collaboration achieved on their NEC project(s) with particular emphasis on clause 10.1 (NEC3) or 10.2 (NEC4).
NEC Sustainability Award of the Year
This award will recognise projects which have set out to reduce their overall impact on the environment in terms of carbon emissions, and /or resilience to climate change in alignment with government carbon reduction targets.
NEC Energy Contract of the Year
An award for any project procured in the energy sector under any NEC Contract. The contracts can be in progress (as long as at least one year has passed). Candidates should give a description of best practice collaboration achieved on their NEC project(s) with particular emphasis on clause 10.1 (NEC3) or 10.2 (NEC4).
NEC Client of the Year
This award is for any client organisation working with an NEC Contract. The client organisation can be from any sector and any country. Candidates should give a description of best practice collaboration achieved with their supply chain on their NEC project(s) with particular emphasis on clause 10.1 (NEC3) or 10.2 (NEC4).
NEC Contract Innovation of the Year
This award will recognise projects demonstrating innovation through use of KPIs, Scope/Works Information/Service Information or additional clause drafting. Entrants should submit their rationale (business needs, supporting localised behavioural change, testing new working methods, anticipated benefit to stakeholders), and the challenges and opportunities presented through this innovation which will be shared as ‘lessons learned’ with the wider Users’ Group.
NEC Contractor of the Year
This award is for any contracting organisation. Candidates should give a description of best practice collaboration achieved on their NEC project(s) with particular emphasis on clause 10.1 (NEC3) or 10.2 (NEC4).
NEC Consultant of the Year
This new award is for any consultancy organisation working with an NEC Contract. The consultancy organisation can be from any sector and any country. Candidates should give a description of best practice collaboration achieved on their NEC project(s) with particular emphasis on clause 10.1 (NEC3) or 10.2 (NEC4).
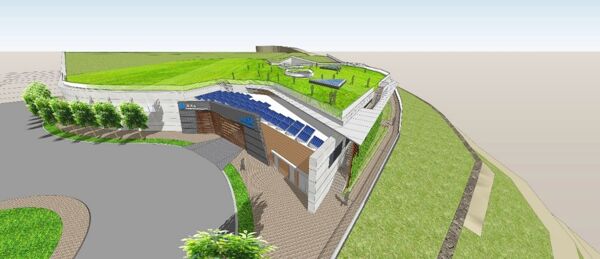
New Prison Programme – Client Designer
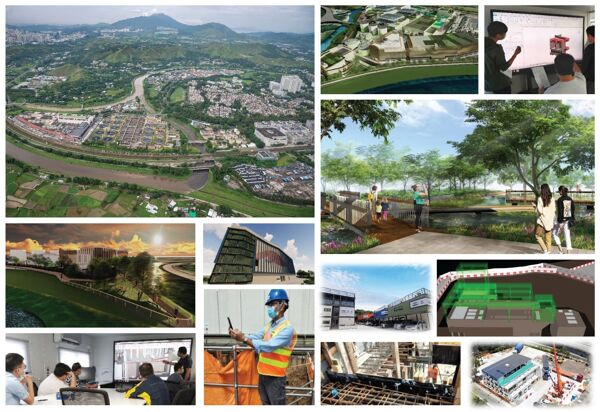
Upgrading of Shek Wu Hui Effluent Polishing Plant
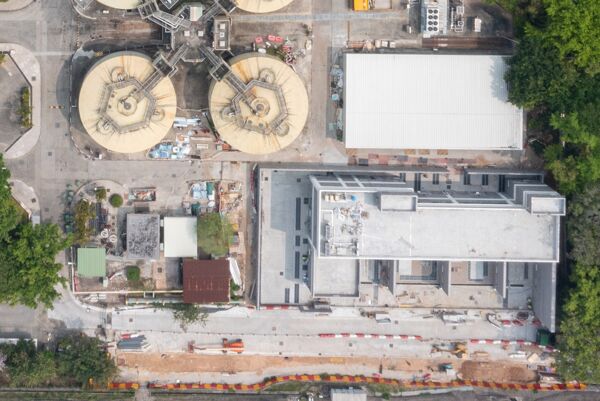
Kwan Lee - Chun Wo Joint Venture
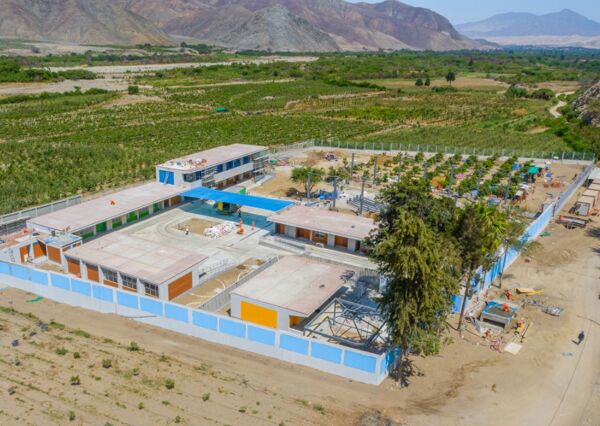
Autoridad para la reconstrucción con cambios (ARCC)
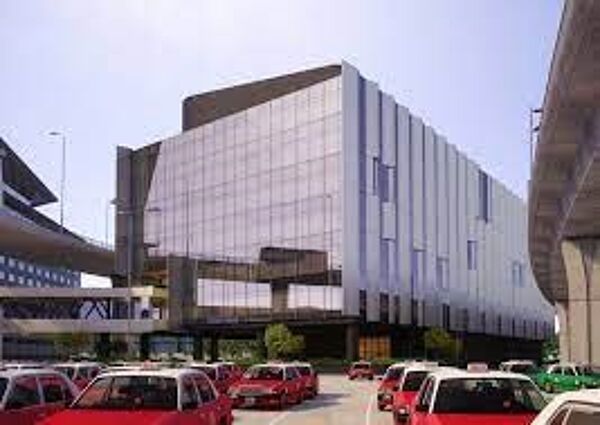
Office Tower Development at HKIA
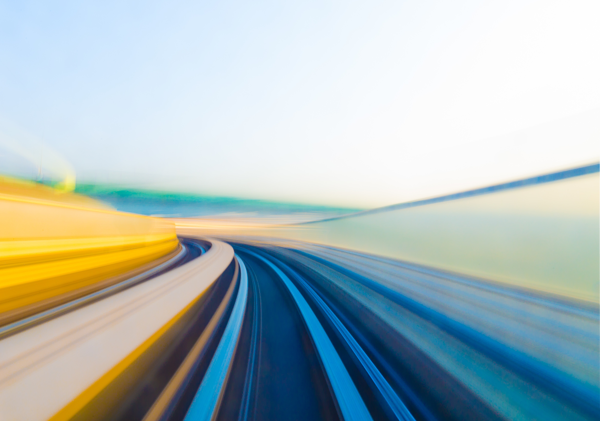
Enhanced monitoring strategies for new railway projects
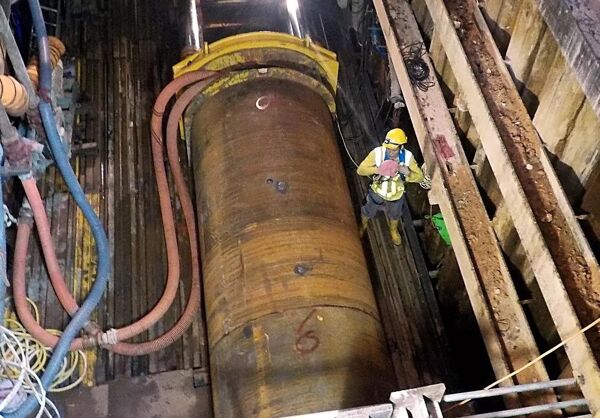
Tung Chung Sewage Rising Main
2022 Shortlist
NEC Building/FM Project of the Year
NEC Client of the Year
- Highways Department
-
Autoridad para la reconstrucción con cambios (ARCC)
- Drainage Services Department
NEC Contract Innovation of the Year
- Collaborative Delivery Framework Programme Incentivisation
-
Upgrading of Shek Wu Hui Effluent Polishing Plant
- Coleraine Campus
NEC Contractor of the Year
- JBA Bentley
- DCK JV (Joint Venture of Daewoo, Chun Wo and Kwan Lee)
-
Kwan Lee - Chun Wo Joint Venture
NEC Sustainability Award of the Year
-
New Prison Programme – Client Designer
- Anderson Road Greywater Treatment Plant
- Newmarket Approach Waste Headquarters
NEC Transport Contract of the Year
- Fanling North New Development Area, Phase 1
- HS2 EWC-S WP007 Camden Heritage
-
Enhanced monitoring strategies for new railway projects
NEC Water Contract of the Year
- Upgrading of Cheung Chau Sewage Treatment and Disposal Facilities
- Hythe Ranges Sea Defences Scheme
-
Tung Chung Sewage Rising Main
Our award categories
NEC Building/FM Project of the Year
An award for any project procured in the building and/or facilities management sector under any NEC Contract. The contracts can be in progress (as long as at least one year has passed). Candidates should give a description of best practice collaboration achieved on their NEC project(s) with particular emphasis on clause 10.1 (NEC3) or 10.2 (NEC4).
NEC Client of the Year
This award is for any client organisation working with an NEC Contract. The client organisation can be from any sector and any country. Candidates should give a description of best practice collaboration achieved with their supply chain on their NEC project(s) with particular emphasis on clause 10.1 (NEC3) or 10.2 (NEC4).
NEC Contract Innovation of the Year
This award will recognise projects demonstrating innovation through use of KPIs, Scope/Works Information/Service Information or additional clause drafting. Entrants should submit their rationale (business needs, supporting localised behavioural change, testing new working methods, anticipated benefit to stakeholders), and the challenges and opportunities presented through this innovation which will be shared as ‘lessons learned’ with the wider Users’ Group.
NEC Contractor of the Year
This award is for any contracting organisation. Candidates should give a description of best practice collaboration achieved on their NEC project(s) with particular emphasis on clause 10.1 (NEC3) or 10.2 (NEC4).
NEC Sustainability Award of the Year
This award will recognise projects which have set out to reduce their overall impact on the environment in terms of carbon emissions, and /or resilience to climate change in alignment with government carbon reduction targets.
NEC Transport Contract of the Year
An award for any project procured in the transport sector under any NEC Contract. The contracts can be in progress (as long as at least one year has passed). Candidates should give a description of best practice collaboration achieved on their NEC project(s) with particular emphasis on clause 10.1 (NEC3) or 10.2 (NEC4).
NEC Water Contract of the Year
An award for any project procured in the water sector under any NEC Contract. The contracts can be in progress (as long as at least one year has passed). Candidates should give a description of best practice collaboration achieved on their NEC project(s) with particular emphasis on clause 10.1 (NEC3) or 10.2 (NEC4).
Expansion of Sha Tau Kok Sewage Treatment Works Phase 1 and Village Sewerage in Tong To
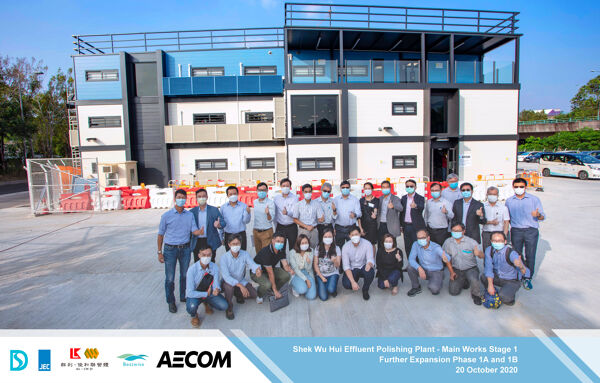
Upgrading of Shek Wu Hui Effluent Polishing Plant
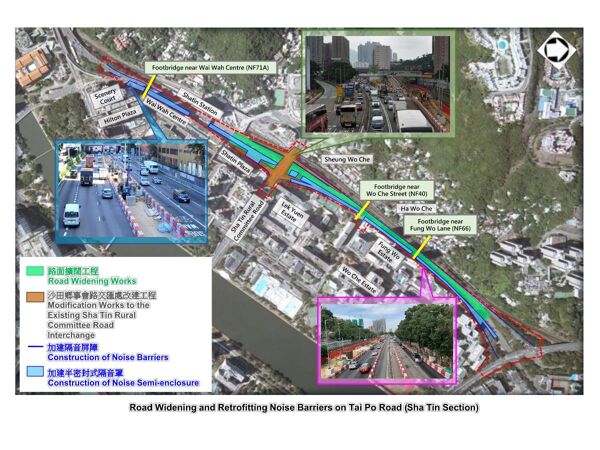
Road Widening and Retrofitting Noise Barriers on Tai Po Road (Sha Tin Section)
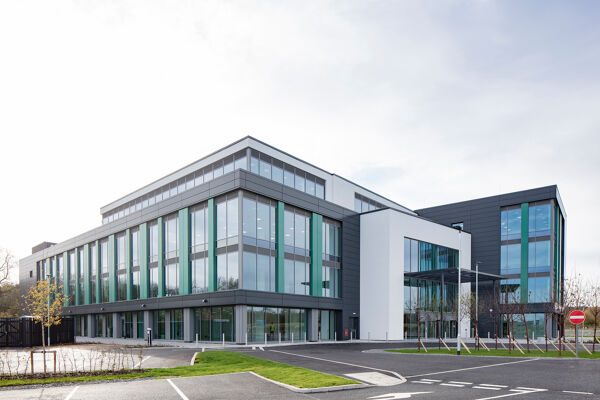
Loughborough University Science Enterprise Park
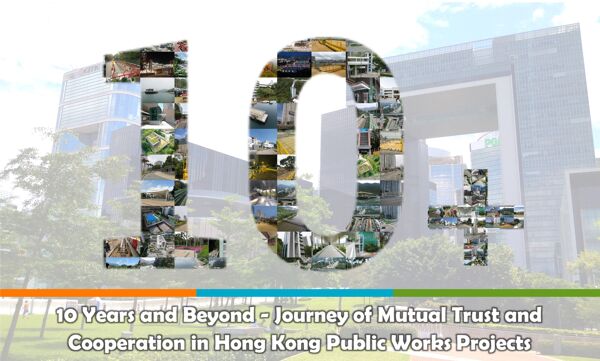
Development Bureau, The Government of the HKSAR
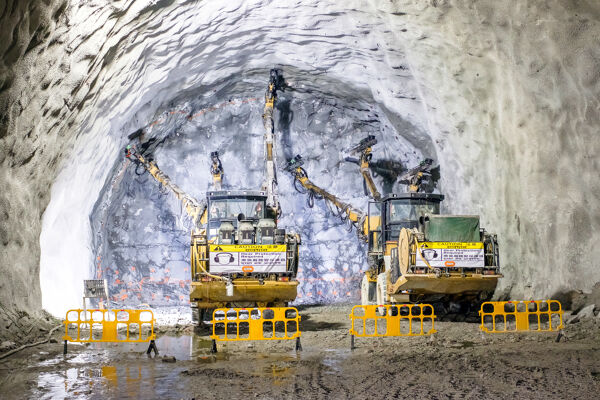
Bouygues Travaux Publics
Finham Gas to Grid
2021 Shortlist
NEC Building/FM Project of the Year
-
Loughborough University Science Enterprise Park
- Design and Construction of a Community Health Centre cum Social Welfare Facilities at Pak Wo Road, North District
- Office Tower Development at Hong Kong International Airport
NEC Client of the Year
-
Development Bureau, The Government of the HKSAR
- Portsmouth City Council
- Rochester Bridge Trust
NEC Contract Innovation of the Year
-
Expansion of Sha Tau Kok Sewage Treatment Works Phase 1 and Village Sewerage in Tong To
- Relocation of Sha Tin Sewage Treatment Works (STSTW) to Caverns
- Drainage Maintenance and Construction in Hong Kong Island and Islands Districts (2021-2025) and Building and Civil Maintenance and Minor Works to DSD Plants and Facilities (2020-2025)
NEC Contractor of the Year
-
Bouygues Travaux Publics
- ATAL-CW-MH Joint Venture
- Kum Shing E&M
NEC Sustainability Award of the Year
-
Finham Gas to Grid
- Expansion of Sha Tau Kok Sewage Treatment Works Phase 1 and Village Sewerage in Tong To
- Tung Chung New Town Extension – Reclamation and Advance Works
NEC Transport Project of the Year
-
Road Widening and Retrofitting Noise Barriers on Tai Po Road (Sha Tin Section)
- Footbridge across Hip Wo Street near the Junction of Hip Wo Street/Mut Wah Street
- West End Project, London Borough of Camden
NEC Water Project of the Year
-
Upgrading of Shek Wu Hui Effluent Polishing Plant
- Relocation of Sha Tin Sewage Treatment Works (STSTW) to Caverns
- Construction of an Additional Sewage Rising Main between Tung Chung and Siu Ho Wan and Associated Works
Our award categories
NEC Building/FM Project of the Year
An award for any project procured in the building and/or facilities management sector under any NEC Contract. The contracts can be in progress (as long as at least one year has passed). Candidates should give a description of best practice collaboration achieved on their NEC project(s) with particular emphasis on clause 10.1 (NEC3) or 10.2 (NEC4).
NEC Client of the Year
An award is for any client organisation working with an NEC Contract. The client organisation can be from any sector and any country.
NEC Contract Innovation of the Year
This award recognises projects demonstrating innovation through use of KPIs, Scope/Works Information/Service Information or additional clause drafting.
NEC Contractor of the Year
This award is for any contracting organisation. Candidates should give a description of best practice collaboration achieved on their NEC project(s) with particular emphasis on clause 10.1 (NEC3) or 10.2 (NEC4)
NEC Sustainability Award of the Year
This is a new award for 2021 that will recognise projects which have set out to reduce their overall impact on the environment in terms of carbon emissions, and /or resilience to climate change in alignment with government carbon reduction targets.
NEC Transport Project of the Year
An award for any project procured in the transport sector under any NEC Contract. The contracts can be in progress (as long as at least one year has passed). Candidates should give a description of best practice collaboration achieved on their NEC project(s) with particular emphasis on clause 10.1 (NEC3) or 10.2 (NEC4)
NEC Water Project of the Year
An award for any project procured in the water sector under any NEC Contract. The contracts can be in progress (as long as at least one year has passed). Candidates should give a description of best practice collaboration achieved on their NEC project(s) with particular emphasis on clause 10.1 (NEC3) or 10.2 (NEC4).
Retrofitting of Noise Barriers on Tuen Mun Road – Town Centre Section
Construction of Dry Weather Flow Interceptor at Cherry Street Box Culvert
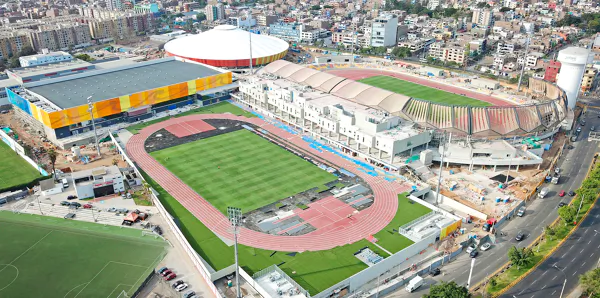
Lima 2019 Pan American and Para Pan American Games
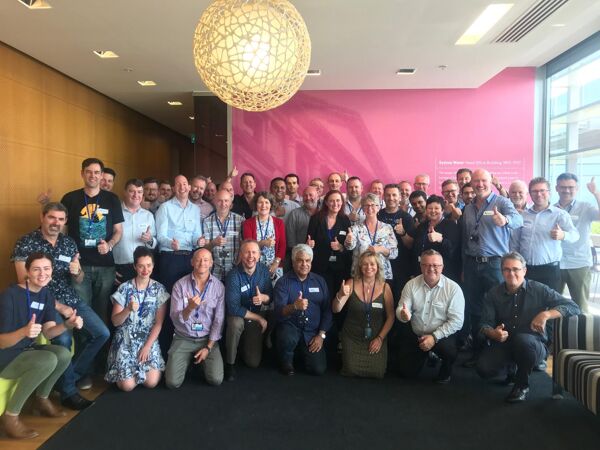
Sydney Water
China State Construction Engineering
Tung Chung New Town Extension – Reclamation and Advance Works
2020 Shortlist
NEC Building/FM Project of the Year
NEC Transport Project of the Year
NEC Water Project of the Year
-
Construction of Dry Weather Flow Interceptor at Cherry Street Box Culvert
- Expansion of Sha Tau Kok Treatment Works Phase 1 and Village Sewerage in Tong To
- Improvement of Water Supply to Sheung Shui and Fanling
NEC Client of the Year
-
Sydney Water
- Lantis
- Civil Engineering and Development Department
NEC Contractor of the Year
-
China State Construction Engineering
- Bouygues Travaux Publics
- Penta-Ocean – Wo Hing Joint Venture
NEC Contract Innovation Award
-
Tung Chung New Town Extension – Reclamation and Advance Works
- Review of Monitoring and Control Strategies for new Railway Projects in Hong Kong
- Expansion of Sha Tau Kok Sewage Treatment Works Phase 1 and Village Sewerage in Tong To
Our award categories
NEC Building/FM Project of the Year
An award for any project procured in the building and/or facilities management sector under any NEC Contract. The contracts can be in progress (as long as at least one year has passed). Candidates should give a description of best practice collaboration achieved on their NEC project(s) with particular emphasis on clause 10.1 (NEC3) or 10.2 (NEC4).
NEC Transport Project of the Year
An award for any project procured in the transport sector under any NEC Contract. The contracts can be in progress (as long as at least one year has passed). Candidates should give a description of best practice collaboration achieved on their NEC project(s) with particular emphasis on clause 10.1 (NEC3) or 10.2 (NEC4)
NEC Water Project of the Year
An award for any project procured in the water sector under any NEC Contract. The contracts can be in progress (as long as at least one year has passed). Candidates should give a description of best practice collaboration achieved on their NEC project(s) with particular emphasis on clause 10.1 (NEC3) or 10.2 (NEC4).
NEC Client of the Year
This award is for any client organisation working with an NEC Contract. The client organisation can be from any sector and any country. Candidates should give a description of best practice collaboration achieved with their supply chain on their NEC project(s) with particular emphasis on clause 10.1 (NEC3) or 10.2 (NEC4).
NEC Contractor of the Year
This award is for any contracting organisation. Candidates should give a description of best practice collaboration achieved on their NEC project(s) with particular emphasis on clause 10.1 (NEC3) or 10.2 (NEC4).
NEC Contract Innovation Award
This award will recognise projects demonstrating innovation through use of KPIs, Scope/Works Information/Service Information or additional clause drafting. Entrants should submit their rationale (business needs, supporting localised behavioural change, testing new working methods, anticipated benefit to stakeholders), and the challenges and opportunities presented through this innovation which will be shared as ‘lessons learned’ with the wider Users’ Group.
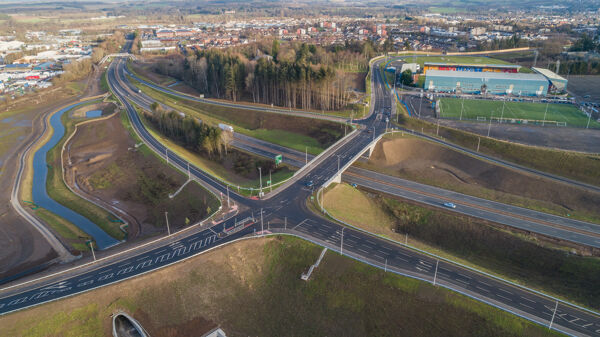
Perth Transport Futures Project Phase 1 – A9 A85 to Bertha Park
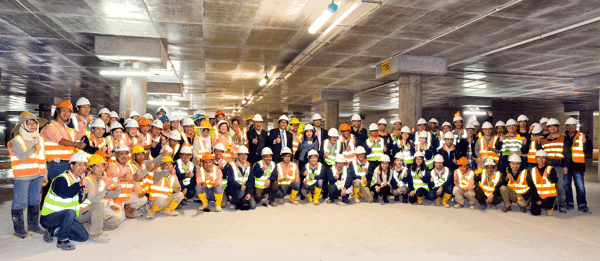
Drainage Services Department
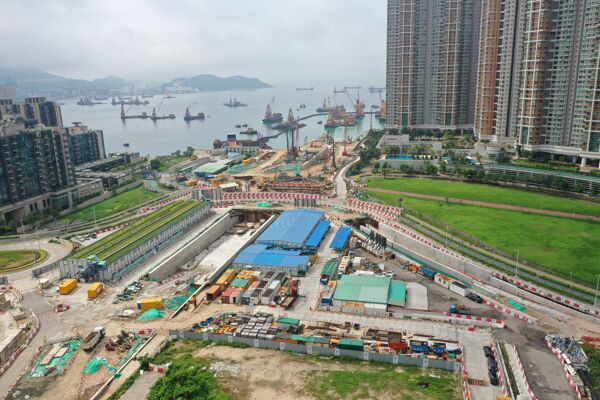
China Road and Bridge Corporation, Build King Joint Venture, Hong Kong
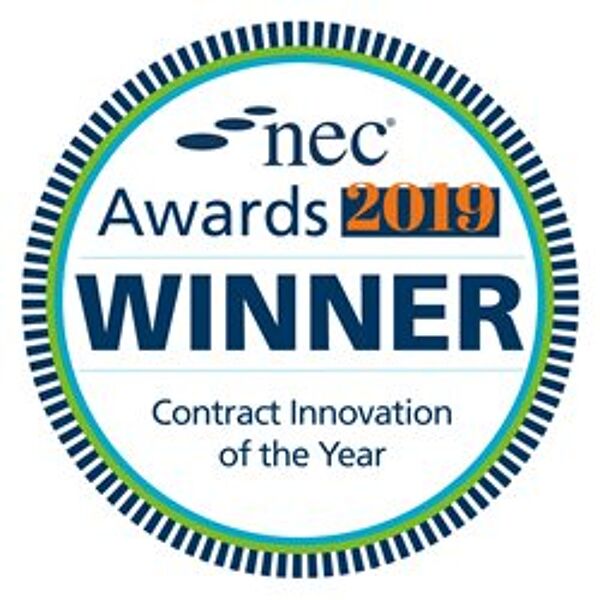
HS2/Arup and Civil Engineering and Design (CDES)
2019 Shortlist
NEC Contract of the Year
NEC Client of the Year
-
Drainage Services Department
- Defence Science Technology Laboratory
- Civil Engineering and Development Department
NEC Contractor of the Year
-
China Road and Bridge Corporation, Build King Joint Venture, Hong Kong
- Access Services (HK) Limited
- China Road and Bridge Corporation
NEC Contract Innovation Award
-
HS2/Arup and Civil Engineering and Design (CDES)
- Clyde Commercial Framework
Our award categories
NEC Contract of the Year
This award is for any project procured under any NEC Contract .The contracts can be in progress (as long as at least one year has passed) any can be from any sector and any country. Particular emphasis is placed on particular emphasis on clause 10.1 (NEC3) or 10.2 (NEC4).
NEC Client of the Year
This award is for any client organisation working with an NEC Contract. The client organisation can be from any sector and any country. Particular emphasis is placed on clause 10.1 (NEC3) or 10.2 (NEC4).
NEC Contractor of the Year
This award is for any contracting organisation. Particular emphasis is placed on clause 10.1 (NEC3) or 10.2 (NEC4).
NEC Contract Innovation Award
This award recognises projects demonstrating innovation through use of KPIs, Scope/Works Information/Service Information or additional clause drafting. The challenges and opportunities presented through these innovations will be shared as ‘lessons learned’ with the wider Users’ Group.
Te Awahou Nieuwe Stroom, Foxton, New Zealand
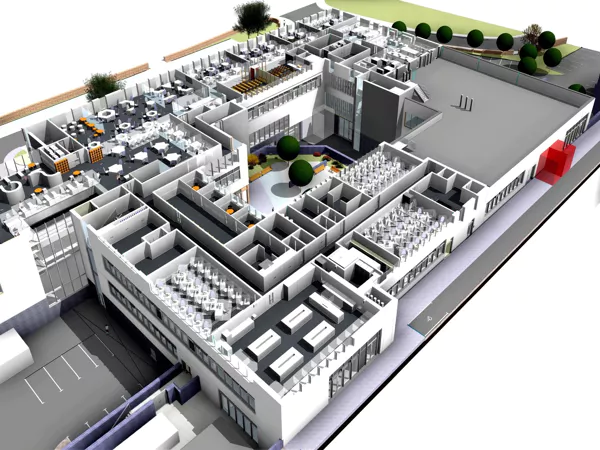
Southern Regional College, Northern Ireland
Hargreaves Industrial Services (HK) Limited
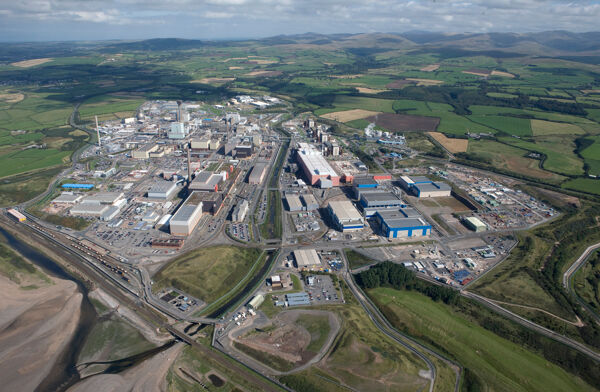
Remediation of Pile 1 East Blower House, United Kingdom
2018 Shortlist
NEC Project of the Year
NEC Client of the Year
-
Southern Regional College, Northern Ireland
- Midlands Highway Alliance, United Kingdom
- Connect Plus, United Kingdom
NEC Contractor of the Year
-
Hargreaves Industrial Services (HK) Limited
- Logan Construction, United Kingdom
- Wang Kee Construction Co. Ltd, Hong Kong
NEC Contract Innovation Award
-
Remediation of Pile 1 East Blower House, United Kingdom
- Generation Auxiliaries Systems Integrated Maintenance Services Contracts
- Quality Construction Supervision and Management for Public Works Projects
Our award categories
NEC Project of the Year
This award is for any project procured under an NEC Contract. Candidates should give a description of best practice collaboration achieved on their NEC project(s) with particular emphasis on clause 10.1 (NEC3) or 10.2 (NEC4).
NEC Client of the Year
This award is for any client organisation. Candidates should give a description of best practice collaboration achieved with their supply chain on their NEC project(s) with particular emphasis on clause 10.1 (NEC3) or 10.2 (NEC4).
NEC Contractor of the Year
This award is for any contracting organisation. Candidates should give a description of best practice collaboration achieved on their NEC project(s) with particular emphasis on clause 10.1 (NEC3) or 10.2 (NEC4).
NEC Contract Innovation Award
This award will recognise innovative additional clause drafting which meets business needs whilst maintaining the critical aspects of the contract including risk profile and mutual collaboration. Entrants should submit their clauses and an outline which should include: rationale for the clause (business needs, supporting localised behavioural change, testing new working methods), anticipated benefit to stakeholders, approach to challenges and opportunities realised through clause in use, lessons to be shared with wider NEC Users’ Group.
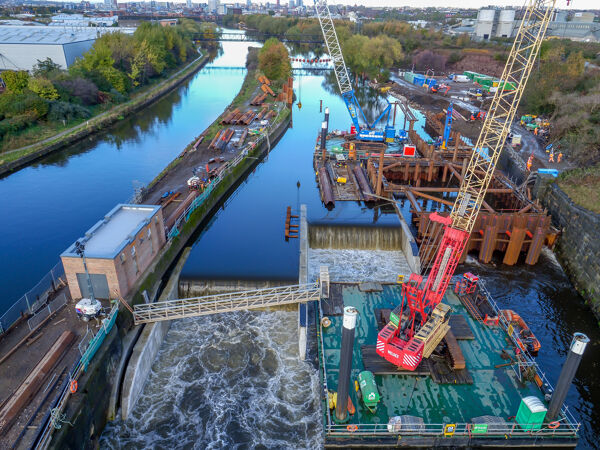
Leeds Flood Alleviation Scheme
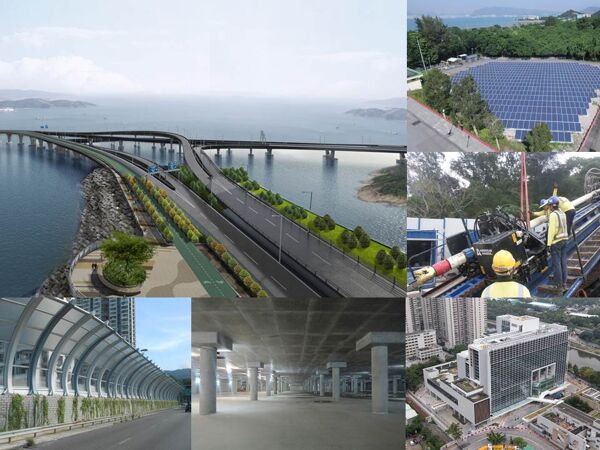
Development Bureau, Government of HKSAR
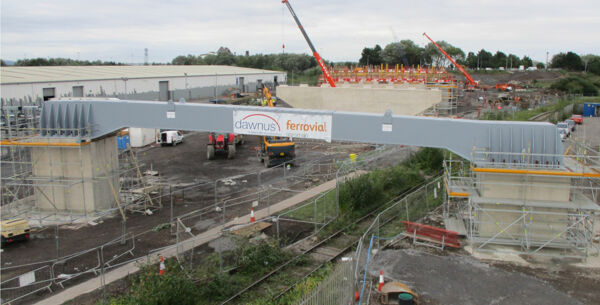
Dawnus Ferrovial Agroman Joint Venture, United Kingdom
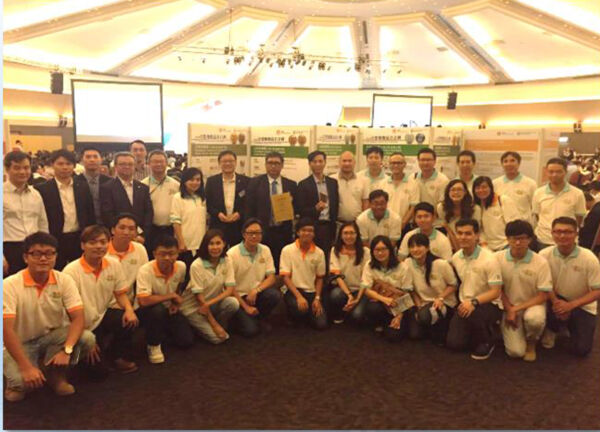
Happy Valley Underground Stormwater Storage Scheme, Hong Kong
2017 Shortlist
NEC Project of the Year
NEC Client of the Year
-
Development Bureau, Government of HKSAR
- Canal and River Trust, United Kingdom
- Environment Agency, United Kingdom
NEC Contractor of the Year
-
Dawnus Ferrovial Agroman Joint Venture, United Kingdom
- Paul Y Construction, Hong Kong
- CRBC - Build King Joint Venture, Hong Kong
NEC Contract Innovation Award
-
Happy Valley Underground Stormwater Storage Scheme, Hong Kong
- Cornwall Growth Deal Infrastructure Improvements Package, United Kingdom
- Additional Clause on Insurance Premium, Hong Kong
Our award categories
NEC Project of the Year
This award is for any NEC project(s). Candidates should give a description of best practice collaboration achieved on their NEC project(s) with particular emphasis on clause 10.1.
NEC Client of the Year
This award is for any client organisation. Candidates should give a description of best practice collaboration achieved with their supply chain on their NEC project(s) with particular emphasis on clause 10.1.
NEC Contractor of the Year
This award is for any contracting organisation. Candidates should give a description of best practice collaboration achieved on their NEC project(s) with particular emphasis on clause 10.1.
NEC Contract Innovation Award
This award recognises innovative additional clause drafting which meets business needs whilst maintaining the critical aspects of the contract including risk profile and mutual collaboration. Entrants should submit their clauses and an outline which should include: rationale for the clause (business needs, supporting localised behavioural change, testing new working methods), anticipated benefit to stakeholders, approach to challenges and opportunities realised through clause in use, lessons to be shared with wider NEC Users’ Group.
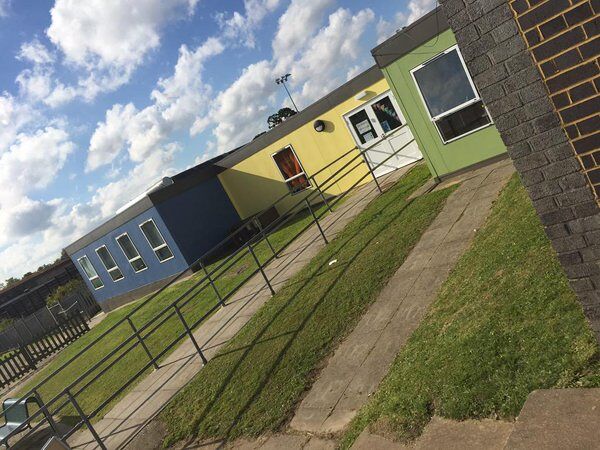
Beanfield and Gretton Primary School
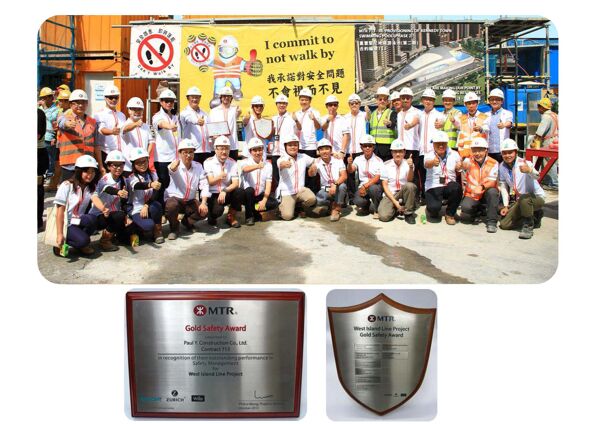
Re-provisioning of Kennedy Town Swimming Pool (Phase 2)
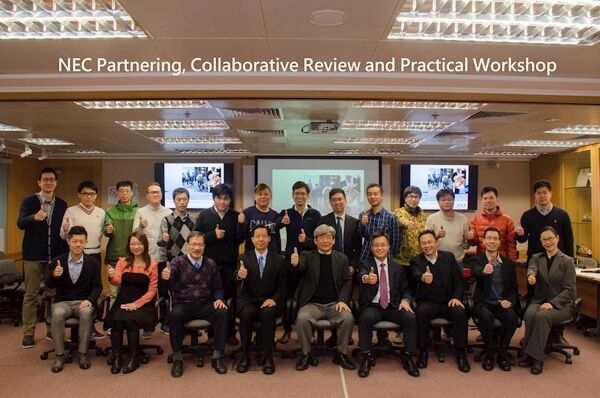
Drainage Services Department
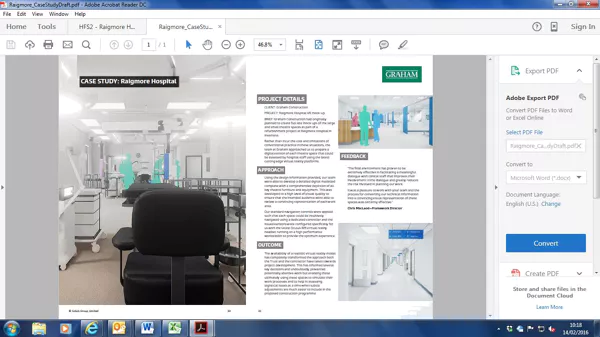
GRAHAM Construction
2016 Shortlist
NEC Small Project of the Year
-
Beanfield and Gretton Primary School
- Oaklands Infant School
- Napsbury Lane Bridge Refurbishment
NEC Large Project of the Year
NEC Client of the Year
-
Drainage Services Department
- Health Facilities Scotland - Frameworks Scotland 2
- Worcestershire Highways Term Contracts
- Environment Agency WEM Framework
NEC Contractor of the Year
-
GRAHAM Construction
- Jackson Civil Engineering - Waterproofing, Enhanced Patch Repairs - M25
Our award categories
NEC Small Project of the Year
This award is for project(s) up to £0.5m. Candidates should give a description of best practice collaboration achieved on their NEC project(s) with particular emphasis on clause 10.1.
NEC Large Project of the Year
This award is for any project(s) over £0.5m. Candidates should give a description of best practice collaboration achieved on their NEC project(s) with particular emphasis on clause 10.1.
NEC Client of the Year
This award is for any client organisation. Candidates should give a description of best practice collaboration achieved with their supply chain on their NEC project(s) with particular emphasis on clause 10.1.
NEC Contractor of the Year
This award is for any contracting organisation. Candidates should give a description of best practice collaboration achieved on their NEC project(s) with particular emphasis on clause 10.1.
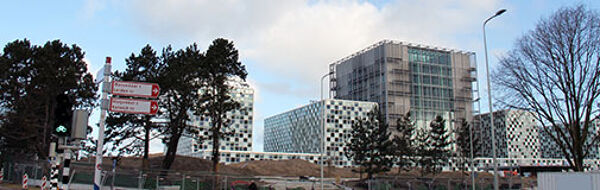
International Criminal Court
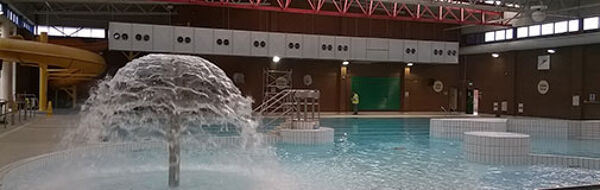
Rushden Splash Pool
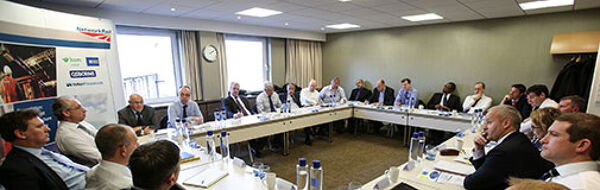
Network Rail
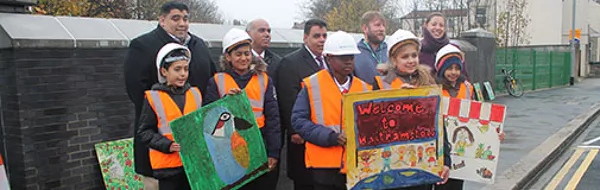
VolkerFitzpatrick
2015 Shortlist
NEC Small Project of the Year
-
Rushden Splash Pool
- Hadleigh Park
- Kennington Park
NEC Large Project of the Year
NEC Client of the Year
NEC Contractor of the Year
-
VolkerFitzpatrick
- Costain
- GRAHAM Construction
Our award categories
NEC Small Project of the Year
This award is for project(s) up to £0.5m. Candidates should give a description of best practice collaboration achieved on their NEC project(s) with particular emphasis on clause 10.1.
NEC Large Project of the Year
This award is for any project(s) over £0.5m. Candidates should give a description of best practice collaboration achieved on their NEC project(s) with particular emphasis on clause 10.1.
NEC Client of the Year
This award is for any client organisation. Candidates should give a description of best practice collaboration achieved with their supply chain on their NEC project(s) with particular emphasis on clause 10.1.
NEC Contractor of the Year
This award is for any contracting organisation. Candidates should give a description of best practice collaboration achieved on their NEC project(s) with particular emphasis on clause 10.1.
Popular links
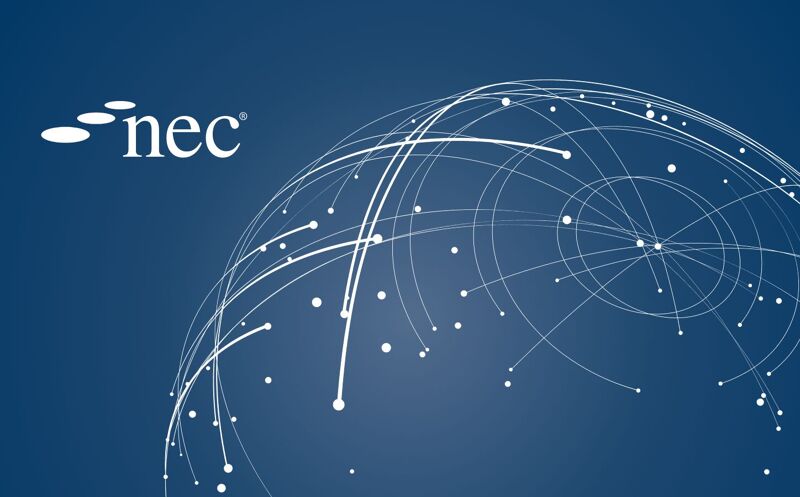
Become a member
Join our global community of NEC users to tap into their expertise and gain support for your latest NEC project.
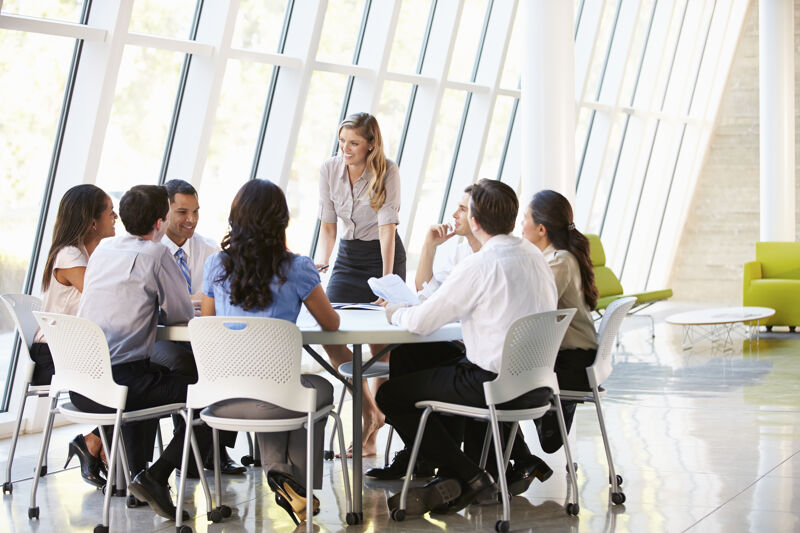
Training
Learn in the classroom or online with NEC training. Whether you are new to NEC or an advanced practitioner, we have a range of training options covering your needs.